The 8-week DIY office fit-out
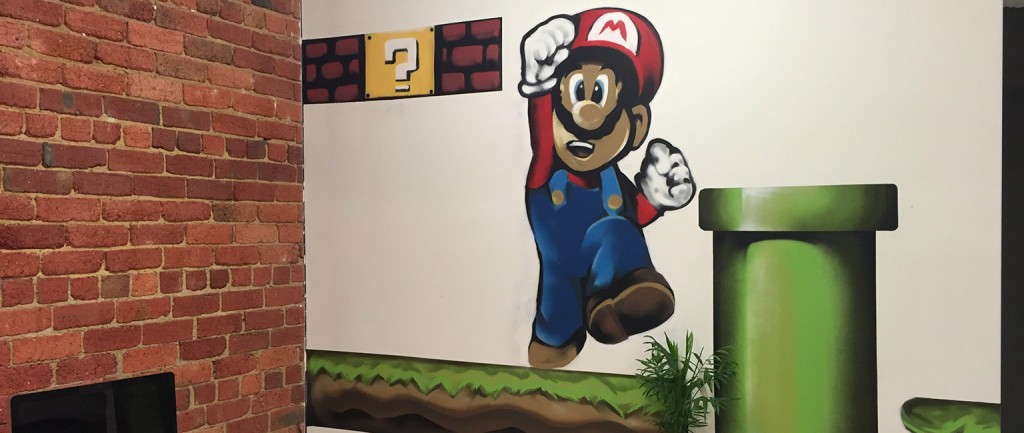
Anyone who’s renovated knows there comes a time when you have to stop researching, accept inconvenience, and move to Stage 2.
In August 2014 the team from Melbourne online marketing firm Optimising – led by bosses James Richardson and Daniel Zuccon – started fitting out their new 256sqm workplace, in Richmond, in readiness for relocating their entire operation in September.
Last week: Part I – The office fit-out 2015
The fit-out job begins
The tech bosses had negotiated with their new landlord collection of the keys to the empty commercial space in July.
Their lease of the empty room began in August and their former lease of a “claustrophobic” space in Cremorne ended in late September.
This created a neat “overlap” of about a week, during which they hoped they could move offices without too much production downtime, explains Richardson, who is also the company’s Sales and Marketing Director.
“It was important that we could get in ahead of time, do our fit-out and then move the team over during a few days so it didn’t have too much impact on workflow,” he says.
Happy to be there: Staff-friendly office fit-outs
A white paint job works well with the exposed brick.
Richardson laughs when asked if any of his techie employees are also qualified tradespeople.
“No, no, definitely not, but, having said that, wherever we could, we’d pick up the tools and myself and my business partner, Daniel, got involved wherever it made sense; we did a lot of painting and desks,” he says.
It was important that we could get in ahead of time so it didn’t have too much impact on workflow.
“Obviously we couldn’t do the construction needed for our kitchenette, meeting room, and electrical works needed to connect the network cabling and high-speed internet connection, and the lighting.
“But we did all the painting – the floors, the roof, everything – and assembled desks; lots of desks.
To save money, Richardson and Zuccon painted for a few hours daily for three weeks including a few weekends.
“We didn’t have a set budget but we were always on a budget, like any small business, we were wary of overcapitalising because we don’t own this building and although we can always take some fittings with us, most of our stuff has been custom built to the space so we didn’t want to spend lots of money we’d never see a return on.”
We were wary of overcapitalising because we don’t own the building.
One of the highlights was bringing in local artist/art student Adam Samarg to co-design and paint all the office’s feature walls. He did the eye-catching works for $600.
A feature wall can brighten up your working environment.
“We just came up with a few ideas and he ran with it and we’re really happy; they really reflect our style.”
DIY: How to make a corporate office feel cosy
According to Richardson, he and Zuccon started their fit-out research two to three months ahead of time because “we knew we’d have to start work because we needed that time to thoroughly search for the best suppliers for our needs”.
“In hindsight it was time well spent because during that time we found ways to save a whole lot of money.”
How did Optimising save money on its fit-out?
Firstly by pricing around, and picking their builder’s brain. Instead of buying finished desk furniture for their open-plan urban office, they custom built desks to their exact needs by ordering measures of laminate sheeting for each top.
Then they bought the exact number of office desk legs needed, rather than committing to a mass volume of 100 legs or more.
“We saved a lot of money on materials because we ordered them directly from the manufacturers rather than buying pre-made from retailers,” Richardson says.
“This saved us more than $1,000 on the desk legs and between $2,000 and $3,000 on the desks.”
Custom building desks allows more room to work with your floor plan.
We saved money on materials by buying from manufacturers not retailers.
Another big saving was the reverse cycle air-conditioners. Two were installed – at the landlord’s expense – after negotiation with his new tenants.
“The place has really big windows, which is great because we love all the natural light and we are pretty insulated because of the full concrete structure, but it also means in the summer we hold the heat so we spoke to the landlord and he was able to install two big reverse-cycle systems, which is a cost saving to us of $1,000s easily.”
Brighten up: Why light and views are good for business
Did everything run to plan during the fit-out?
Yes, except for water pouring down the walls whenever it rained.
“Our rooftop terrace was one of the big attractions of leasing this space, we were all like ‘wow’ when we saw it.
“But we have had a few issues with roof leaks. Basically the rainwater started coming through the walls and roof whenever we had a big downpour, which was a bit concerning although luckily nothing was damaged.
“The building’s owner has had to do a bit of work in recent months to lay a new waterproofing membrane and it’s set our plans back for the roof top until that work is complete although it looks like we will get up there in coming weeks to install the rooftop benches and deck we’ve planned, so that’s very exciting.
“We’ve already got the BBQ up there in place and ready to go.”
Next week we take a look at the final cost breakdown and unveil the new look for this long-forgotten commercial space.